Lathe Machining Parts Manufacturers: Elevating Manufacturing Excellence
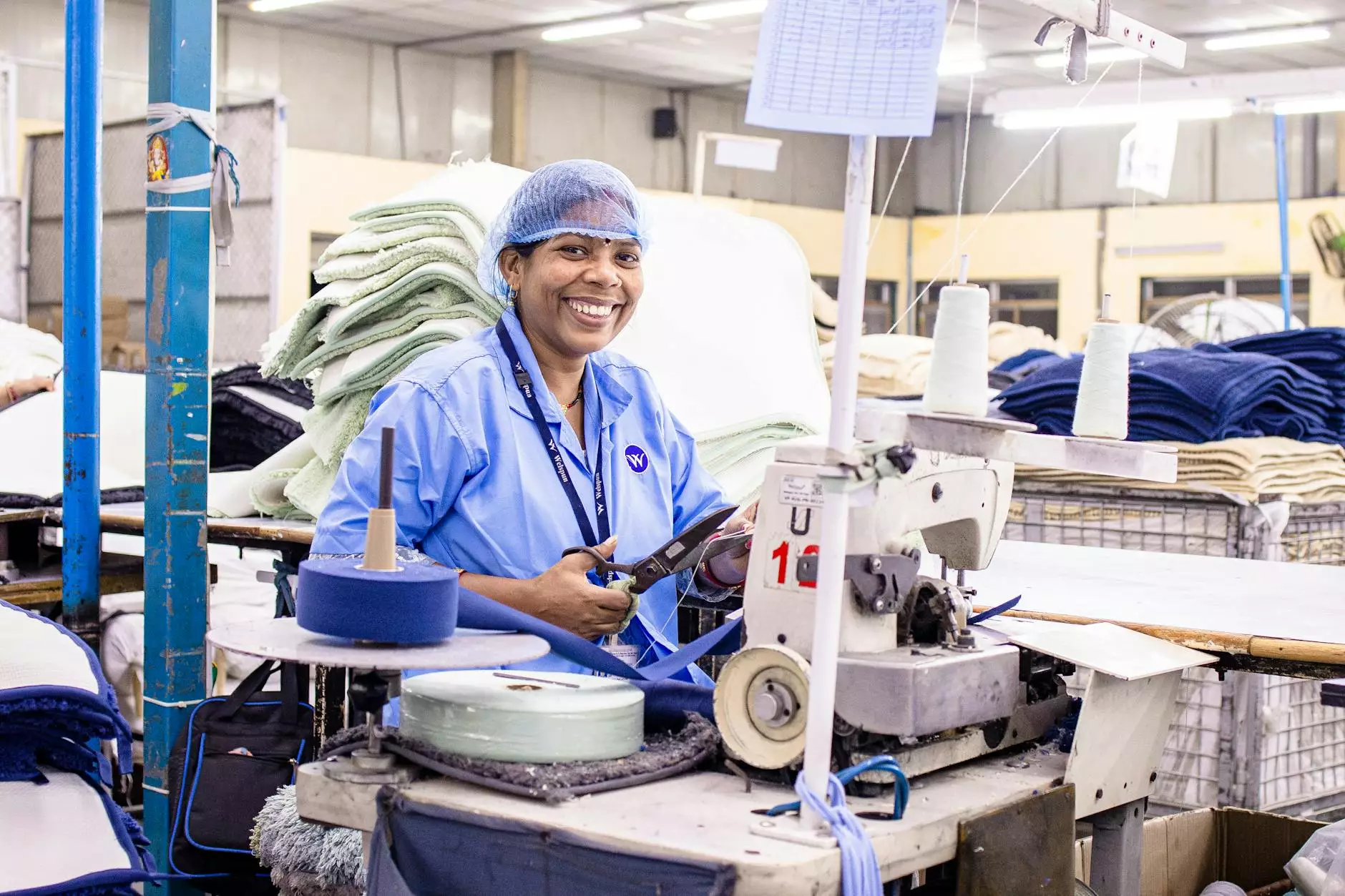
The manufacturing industry has been experiencing significant changes and innovations over the years. Among these advancements, lathe machining stands out as a critical process that shapes various components used in numerous applications. This article delves deep into the realm of lathe machining parts manufacturers, their importance, processes, and the value they bring to the manufacturing sector.
Understanding Lathe Machining
Lathe machining is a fundamental process in manufacturing where a rotating workpiece is shaped using cutting tools. The versatility of lathe machines allows for a broad range of applications, from producing simple cylindrical parts to complex geometries.
Key Features of Lathe Machines
- Rotational Motion: The workpiece is rotated while a stationary cutting tool removes material, creating a desired shape.
- Precision: Lathe machining offers high precision, ensuring tight tolerances are maintained.
- Versatility: Designed to handle various materials, including metals, plastics, and wood, lathe machines can be adapted for various tasks.
- Efficiency: Automated lathes and CNC technology allow for high production rates and reduced manual effort.
The Role of Lathe Machining Parts Manufacturers
Lathe machining parts manufacturers play a vital role in the supply chain of numerous industries, including automotive, aerospace, electronics, and medical devices. They produce an extensive range of components that serve as essential elements in larger assemblies.
Why Choose a Specialized Manufacturer?
Working with specialized lathe machining parts manufacturers guarantees quality, precision, and expertise. Here are some reasons to consider when selecting a manufacturer:
- Expert Knowledge: Specialized manufacturers often have years of experience and can provide insights that enhance product design and functionality.
- Quality Assurance: Reputable manufacturers implement rigorous quality control processes to ensure that every component meets industry standards.
- Customization: Many manufacturers offer customization options tailored to the specific needs of their clients, which enhances product performance.
- Cost-Effectiveness: Collaborating with experienced manufacturers can lead to cost efficiencies due to optimized processes and reduced waste.
Processes Involved in Lathe Machining
Understanding the processes involved in lathe machining is crucial for appreciating the capabilities of lathe machining parts manufacturers. Here are some of the key machining processes:
1. Turning
Turning involves the removal of material from the outer diameter of a rotating workpiece. It's pivotal for creating cylindrical shapes and is achieved using a single-point cutting tool.
2. Facing
Facing is the process where the end of a workpiece is machined flat. This is important for ensuring that components fit together correctly in assemblies.
3. Threading
Threading creates screw threads on a workpiece, which is essential for the fastening of components. This intricate process can be accomplished via various threading tools and techniques.
4. Boring
Boring is used to enlarge existing holes on a workpiece, enhancing precision and often required in hydraulic and pneumatic applications.
Materials Used in Lathe Machining
Lathe machining can be performed on several types of materials, including:
- Metals: Steel, aluminum, brass, and titanium are common materials due to their durability and strength.
- Plastics: Materials like polycarbonate and nylon are often machined for lighter components.
- Composites: Advanced materials that combine different properties are increasingly used in specialized applications.
The Advantages of Working with Lathe Machining Parts Manufacturers
Choosing to partner with experienced lathe machining parts manufacturers can provide numerous benefits:
- Enhanced Performance: High-quality machined parts lead to improved overall performance of the final products.
- Increased Longevity: Well-manufactured components tend to have a longer lifespan, resulting in cost savings for businesses over time.
- Advanced Technology: Many modern manufacturers utilize state-of-the-art CNC lathes and technology, ensuring precise outputs.
- Fast Turnaround: Because manufacturers have streamlined processes, they can often deliver parts faster than smaller operations.
How to Choose the Right Lathe Machining Parts Manufacturer
When selecting a manufacturer, consider the following factors:
1. Reputation
Research potential manufacturers, read reviews, and seek recommendations to gauge their reputation in the market.
2. Certifications
Ensure that the manufacturer meets relevant industry standards and certifications, which can serve as a benchmark for quality.
3. Technology and Equipment
Inquire about the type of machinery the manufacturer uses. Modern, high-quality equipment usually leads to better outputs.
4. Capabilities
Ensure the manufacturer can handle the specific requirements of your project, including material types and dimensions.
Future Trends in Lathe Machining
The landscape of lathe machining is evolving rapidly. Here are some trends to watch:
- Integration of AI: Artificial intelligence is being used to optimize machining processes, enhancing efficiency and reducing waste.
- Automation: More manufacturers are adopting fully automated systems for increased productivity and accuracy.
- Sustainability: There's a growing emphasis on using sustainable practices and materials in the manufacturing process.
Conclusion
As we have explored, lathe machining parts manufacturers play a crucial role in various industries by providing quality components that meet specific needs. By understanding the processes, advantages, and selecting the right partners, businesses can significantly enhance their manufacturing capabilities. The future of lathe machining is bright, with advancements in technology continuing to improve efficiency and effectiveness. For those seeking reliable and high-quality machining services, deepmould.net stands as a testament to excellence in the industry.