Understanding the Parts of a CNC Lathe: A Comprehensive Guide
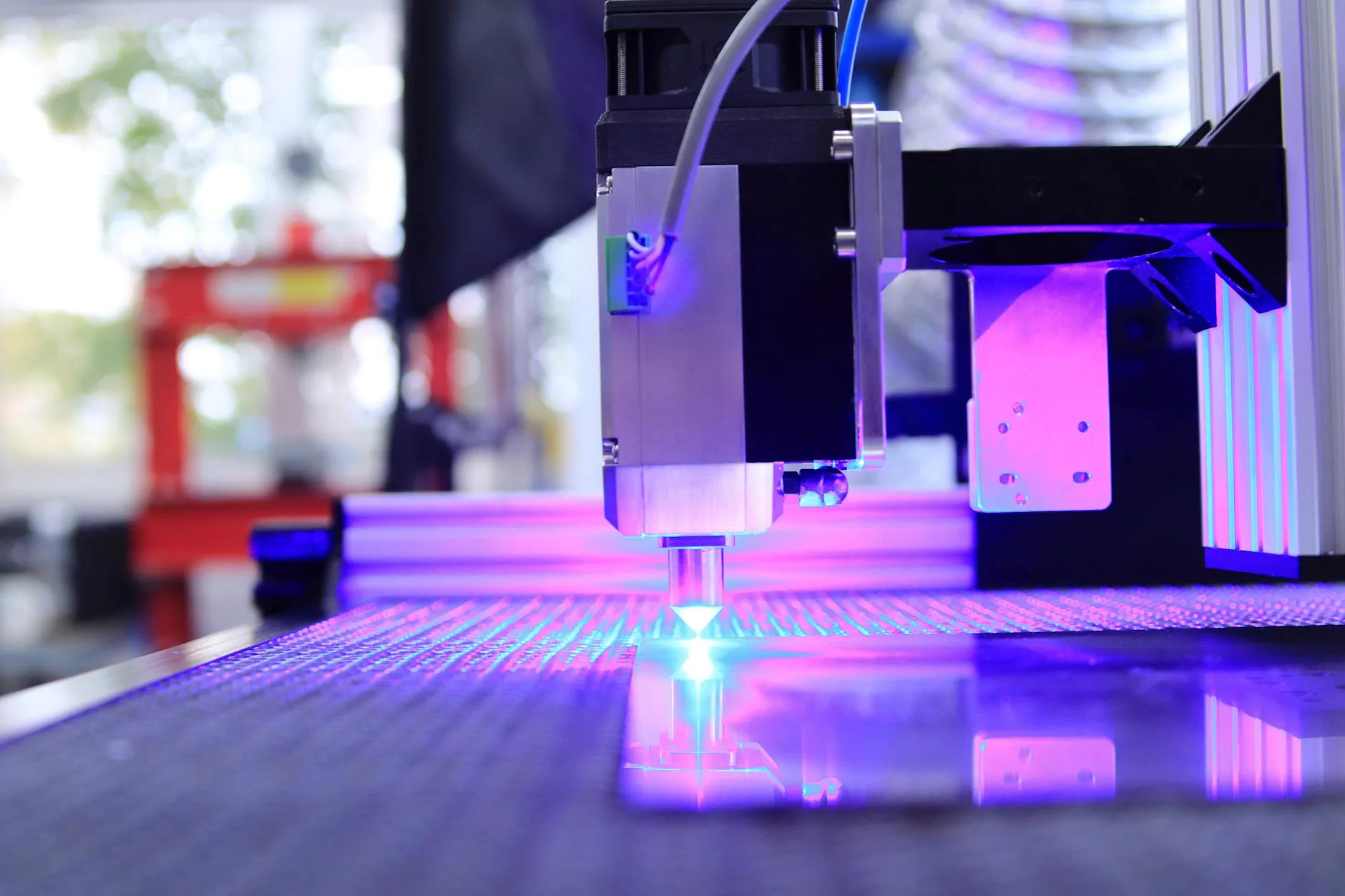
In the realm of modern manufacturing, CNC lathes stand as critical machines that enable precision and efficiency in production. As a segment of the metal fabrication industry, understanding the parts of a CNC lathe is essential for engineers, operators, and anyone interested in mastering the art of machining. This article will provide an in-depth exploration of each component of a CNC lathe, its functions, and its relevance in the context of advanced manufacturing processes.
The Importance of CNC Lathes in Metal Fabrication
Before diving into the specifics of the parts of a CNC lathe, it is vital to grasp why these machines are integral to metal fabrication. CNC, or Computer Numerical Control, refers to the automation of machine tools through computers executing pre-programmed sequences of machining operations. This technology has revolutionized the fabrication industry by allowing for:
- Increased Precision: CNC lathes produce highly accurate and repeatable parts with minimal human intervention.
- Enhanced Productivity: With the ability to run jobs unattended, CNC lathes significantly reduce production time.
- Complex Shapes and Designs: CNC lathes can create intricate shapes that would be impossible or highly difficult to achieve manually.
- Consistency: Parts produced by CNC lathes maintain uniform quality, crucial for large-scale production.
Key Parts of a CNC Lathe
The following sections will detail the main components of a CNC lathe, explaining how each part contributes to the machine's overall functionality and efficiency in the metal fabrication process. Understanding these components will not only enhance operational efficiency but also facilitate better maintenance and troubleshooting.
1. The Base
The base of a CNC lathe is the heavy, stable foundation that supports all other components. It is typically constructed from cast iron or another heavy material to absorb vibrations during operation. A robust base is crucial for maintaining precision, as any movement can lead to inaccuracies in machining.
2. The Bed
The bed is where the carriage, tailstock, and other parts are mounted. It features guideways that ensure the smooth movement of the carriage as it traverses the bed. The alignment and surface finish of the bed are critical for the accurate machining of parts.
3. The Headstock
The headstock houses the spindle, the motor, and the transmission system, which powers the lathe and holds the workpiece. Key functions of the headstock include:
- Spindle: The spindle rotates the workpiece at high speeds, essential for precision machining.
- Chuck: The chuck clamps the workpiece securely, ensuring that it does not move during the machining process.
- Feed Mechanism: This mechanism controls the advancement of the tool relative to the workpiece, allowing for precise cutting.
4. The Tailstock
The tailstock is positioned opposite the headstock and can be moved along the bed. It provides support for the other end of the workpiece, especially for longer components. In addition to providing stability, the tailstock often houses a drill or other tools for additional machining operations.
5. The Cross Slide
The cross slide is a critical component that moves perpendicular to the workpiece's axis. It accommodates the cutting tool and allows for fine adjustments during machining. The precision of the cross slide is vital for producing detailed features on the workpiece.
6. The Tool Post
The tool post holds the cutting tools securely in place. Various types of tool posts are available, including manual and indexing types. The choice of tool post can affect the speed and quality of the machining process. Quality tool posts maintain tool alignment and reduce vibrations during cuts.
7. The CNC Control System
The CNC control system is the brain of the CNC lathe, executing programmed instructions to control the movement of the machine. It interprets G-code, a language that tells the lathe precisely how to move. Key features of a modern CNC control system include:
- User Interface: Modern systems provide intuitive interfaces for easy programming and operation.
- Feedback Systems: Feedback loops allow the machine to make real-time adjustments for improved accuracy.
- Data Logging: Many systems can log production data for analysis and optimization of processes.
8. The Servomotors and Drives
The servomotors and drives are essential for converting electrical signals from the CNC control system into precise movements of the lathe components. These components ensure that every movement is accurate and that transitions between operations are smooth, enhancing overall efficiency.
9. The Coolant System
The coolant system is crucial for maintaining optimal operating temperatures during machining. It helps in:
- Reducing Heat: Excessive heat can warp components and reduce tool life.
- Improving Tool Life: By keeping tools cool, the coolant system prolongs their lifespan and maintains cutting efficiency.
- Enhancing Surface Finish: Proper cooling can lead to smoother finishes on the machined parts.
10. Safety Features
Modern CNC lathes incorporate various safety features to protect operators and machinery. These may include:
- Emergency Stops: Easily accessible stops to halt the machine quickly in case of a malfunction.
- Guarding: Protective covers around moving parts to prevent injury.
- Hazard Sensors: Systems that detect unsafe operating conditions and immediately shut down the lathe.
Maintenance of CNC Lathes
To ensure the longevity and performance of CNC lathes, regular maintenance is indispensable. Key maintenance tasks include:
- Lubrication: Regularly lubricating parts reduces friction and wear.
- Cleaning: Keeping the machine clean prevents debris from affecting precision.
- Calibration: Periodic calibration is necessary to maintain accuracy over time.
- Inspection: Regular inspections can identify potential issues before they lead to breakdowns.
Conclusion
Understanding the parts of a CNC lathe is key to leveraging its capabilities in metal fabrication effectively. Each component, from the base to the CNC control system, plays a vital role in producing high-quality machined parts. By embracing the intricacies of CNC lathes, businesses like Deep Mould can ensure they stay at the forefront of the manufacturing industry, maximizing efficiency, precision, and ultimately, profitability. As technology continues to advance, staying informed about CNC technology and its components will only become more critical for success in the competitive field of metal fabrication.