CNC Machining Parts: Revolutionizing Metal Fabrication
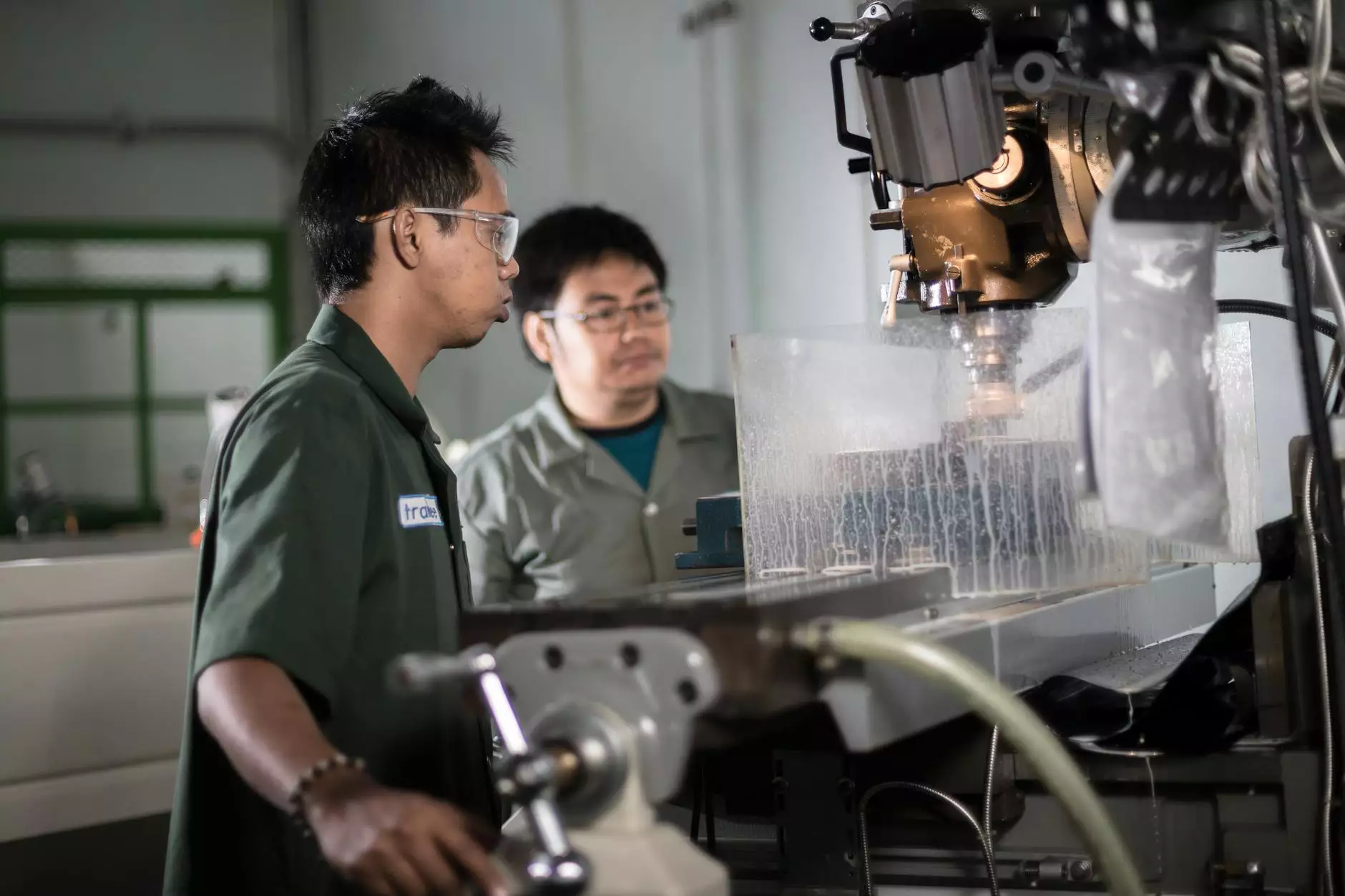
In today's fast-paced manufacturing environment, CNC machining parts offer unparalleled precision and efficiency. As industries across the globe seek to enhance their production capabilities, CNC machining has emerged as a cornerstone of modern metal fabrication. This comprehensive article will delve into the intricacies of CNC machining, its benefits, applications, and why businesses, particularly those in the realm of metal fabrication, should consider integrating this technology into their operations.
Understanding CNC Machining: The Basics
CNC, or Computer Numerical Control, machining is a process that utilizes computer software to control machine tools. These machine tools include lathes, mills, routers, and grinders, which can create intricately designed parts with exceptional accuracy. The methodology employs various material types, from metals like aluminum, steel, and titanium to plastics and composites.
How CNC Machining Works
The CNC machining process begins with the creation of a 3D CAD model (Computer-Aided Design). This model is then translated into CNC code, which consists of a series of commands that instruct the CNC machine on how to move and cut the material. The fundamental steps involved in CNC machining include:
- Designing the Part: Engineers create a detailed CAD model of the part that needs to be manufactured.
- Generating CNC Code: Using CAM (Computer-Aided Manufacturing) software, the CAD model is converted into CNC code that the machine can understand.
- Setting Up the Machine: The operator loads the material onto the machine, secures it, and inputs the CNC code.
- Machining the Part: The CNC machine executes the code, precisely cutting the material into the desired shape over the course of various operations.
- Finishing Touches: After the machining process, parts may undergo additional processes such as polishing, coating, or assembly.
Advantages of CNC Machining Parts in Metal Fabrication
The integration of CNC machining parts into manufacturing processes brings numerous advantages, making it a vital component in metal fabrication.
1. Precision and Accuracy
One of the most significant benefits of CNC machining is its ability to produce parts with exceptional precision and consistency. The automated process reduces the likelihood of human error, ensuring that each part manufactured meets stringent specifications. This level of accuracy is particularly vital in industries such as aerospace and medical device manufacturing, where tolerances can be critical.
2. Enhanced Production Efficiency
CNC machining machines operate at high speeds and can run continuously, significantly enhancing production rates. This efficiency translates to lower labor costs and faster turnaround times, allowing companies to meet rising demand without compromising quality.
3. Flexibility and Customization
CNC technology allows for the easy reprogramming of machines to create different parts without the need for extensive setup changes. This flexibility means manufacturers can quickly adapt to new design requirements or customer demands, making it an excellent solution for custom parts production.
4. Reduced Waste
By utilizing advanced cutting techniques, CNC machining minimizes material waste, which is not only cost-effective but also environmentally friendly. Efficient material usage is crucial for companies looking to reduce their environmental footprint while optimizing profits.
5. Complex Geometries Made Easy
CNC machines can create complex shapes and intricate designs that would be nearly impossible to achieve with traditional machining methods. This capability opens new possibilities for innovation in product design and engineering.
Applications of CNC Machining Parts
The versatility of CNC machining parts allows for applications across a wide range of industries. Here are some notable sectors that heavily rely on CNC machining:
Aerospace Industry
CNC machining is paramount in the aerospace industry, where components must adhere to strict safety and performance standards. Parts such as engine mounts, landing gear, and brackets are often produced using CNC machining due to their complex geometries and the need for high precision.
Automotive Industry
The automotive sector utilizes CNC machined parts for everything from engine components to chassis parts. The ability to produce lightweight yet durable parts can help improve a vehicle's overall performance and fuel efficiency.
Medical Devices
In the medical field, CNC machining ensures that essential devices such as surgical instruments and implants are manufactured to exact specifications, allowing for safe and effective patient care. The precision of CNC machining is crucial for products that require sterility and reliability.
Consumer Electronics
CNC machining also finds applications in the consumer electronics industry, where it creates components for devices such as smartphones, computers, and home appliances. The ability to produce small, intricate parts is vital for modern device manufacturing.
Impact of CNC Machining on the Future of Manufacturing
As technology continues to evolve, CNC machining stands at the forefront of manufacturing innovation. With advancements in automation, robotics, and artificial intelligence, the capabilities of CNC machining are expanding, leading to even greater efficiency and precision.
1. Integration with Additive Manufacturing
Additive manufacturing, or 3D printing, is gaining ground as a complementary process to CNC machining. By combining both technologies, manufacturers can capitalize on the benefits of rapid prototyping through additive methods while achieving high-quality finishes and precision with CNC machining.
2. Smart Manufacturing and Industry 4.0
The advent of Industry 4.0 is bringing about a revolution in how manufacturing processes are managed. By utilizing the Internet of Things (IoT), CNC machines can become smarter, with the ability to communicate data in real-time for proactive maintenance, monitoring performance, and optimizing operations.
3. Customized Solutions on Demand
As market demands shift towards personalized products, CNC machining can offer bespoke solutions efficiently. The technology's agility allows manufacturers to produce customized parts quickly, thus meeting specific customer requirements without the traditional lead times.
Choosing the Right CNC Machining Service
1. Expertise and Experience
Choose a company that has a solid track record and specialization in CNC machining parts relevant to your industry. The more experience they have, the better understanding they will possess of material properties and processes.
2. Technology and Equipment
Inquire about the type of CNC machines and technologies the provider utilizes. State-of-the-art equipment can significantly enhance part quality and production efficiency.
3. Quality Control Processes
Ensure the service provider has rigorous quality control measures in place. Certifications such as ISO 9001 are indicative of a commitment to maintaining high-quality standards.
4. Turnaround Times
Discuss lead times and the company’s capacity to meet deadlines. Timely delivery is crucial for maintaining production schedules in your business.
5. Customer Support
Consider the level of customer service offered. A responsive provider can make a difference in resolving challenges and ensuring smooth operations throughout the manufacturing process.
Conclusion
CNC machining parts redefine what's possible in the world of metal fabrication by bringing together technology, precision, and efficiency. Businesses that embrace CNC machining will not only gain a competitive edge through enhanced productivity and accuracy but also position themselves for future growth and innovation. As the manufacturing landscape continues to evolve, CNC machining will undoubtedly remain a pivotal element in delivering high-quality products across various industries. For companies looking to explore CNC machining solutions, partnering with an experienced provider like deepmould.net would be a wise decision, ensuring that they harness the full potential of this groundbreaking technology.